Club member Henry Howard gave his first demo this evening, and it was a somewhat unusual one with a humourous background.
He made an (all-seeing?) eyeball mounted on a pedestal, something that he originally did for an opthalmic surgeon who had treated him. Comprised of three main pieces, he carried out the turning on his own lathe, mostly with the aid of small chucks for mounting the wood.
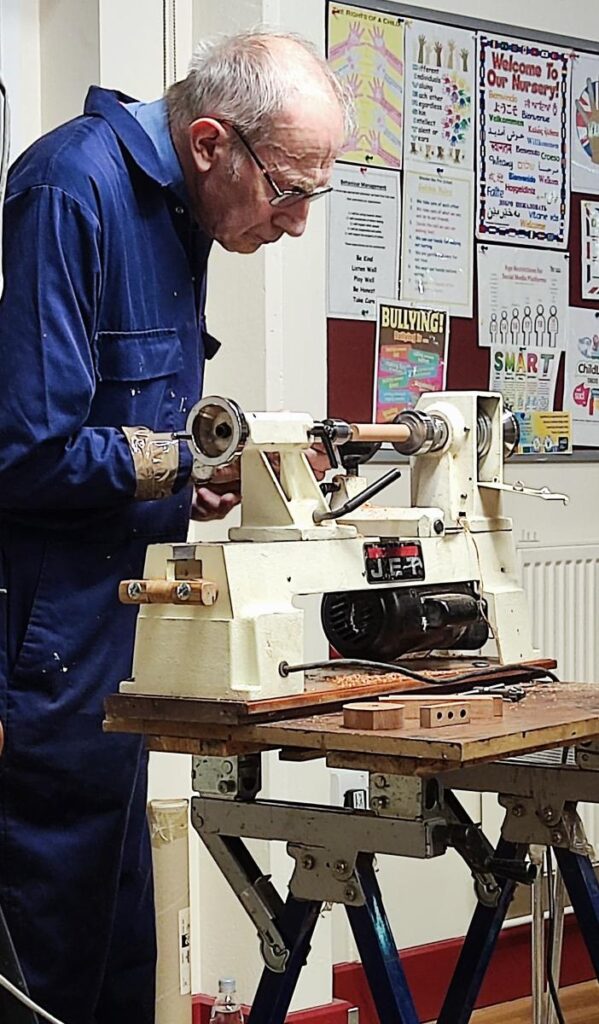
Stem
The square blank, approx 150mm x 25mm was mounted between centres and brought to round, and then a tenon put on one end – the size of which Henry checked in a little test piece that he had brought along.
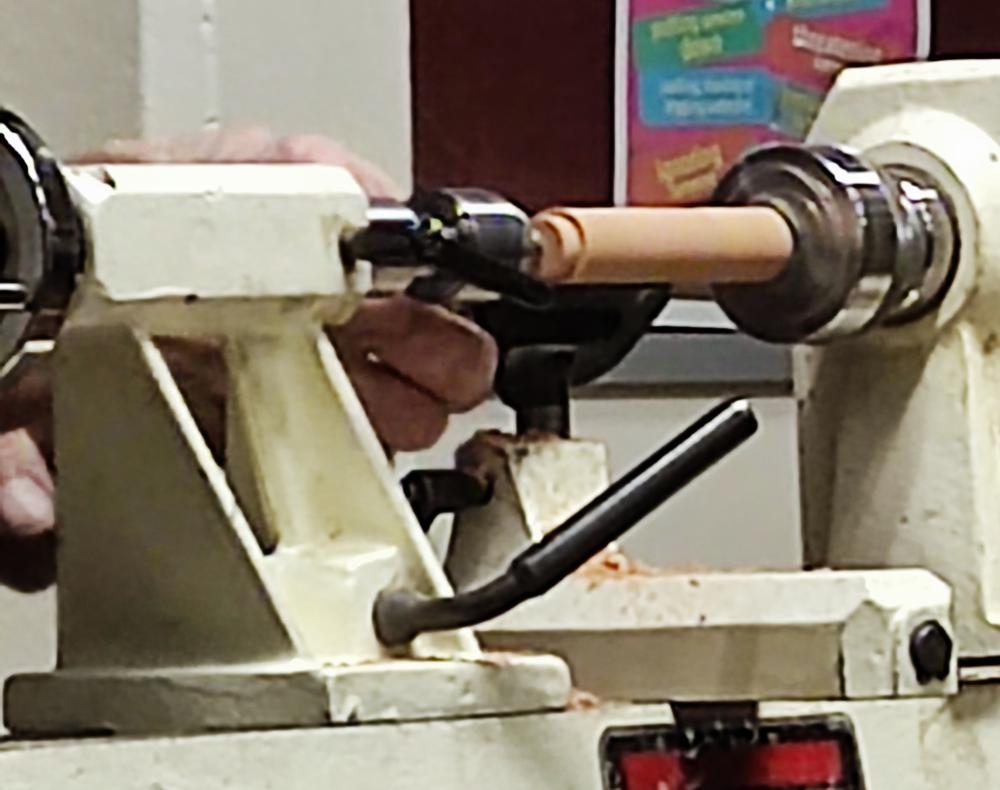
It was then mounted in the chuck, supported by the tailstock, and a 7mm tenon formed on the end.
With this done, Henry added some shape and detail to the stem before sanding through the grits and applying friction polish.
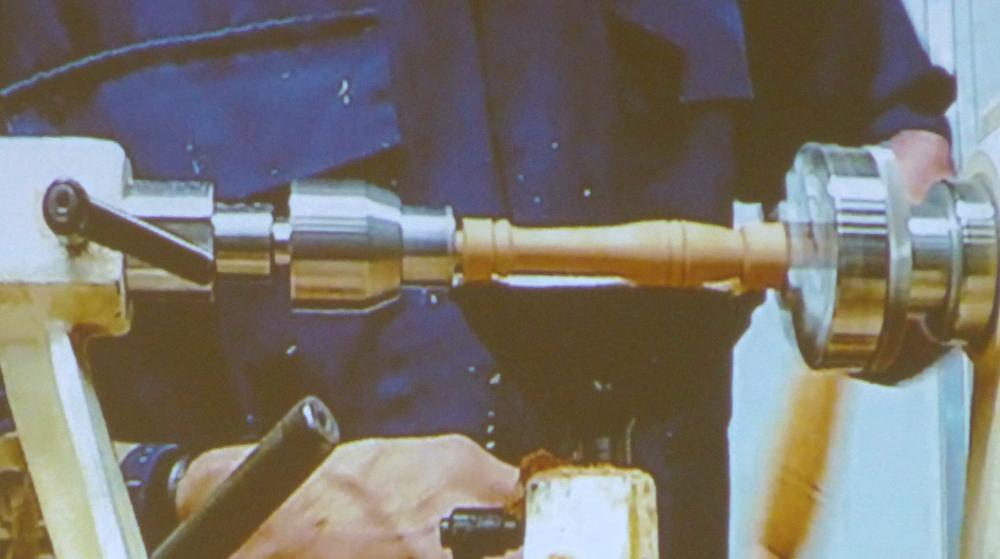
Base
The blank for this was mounted on a screw chuck, trued up, and the circumference sanded. The disk was dished slightly, as this will be the underside of the base, and he turned a rounded profile for the top edge.
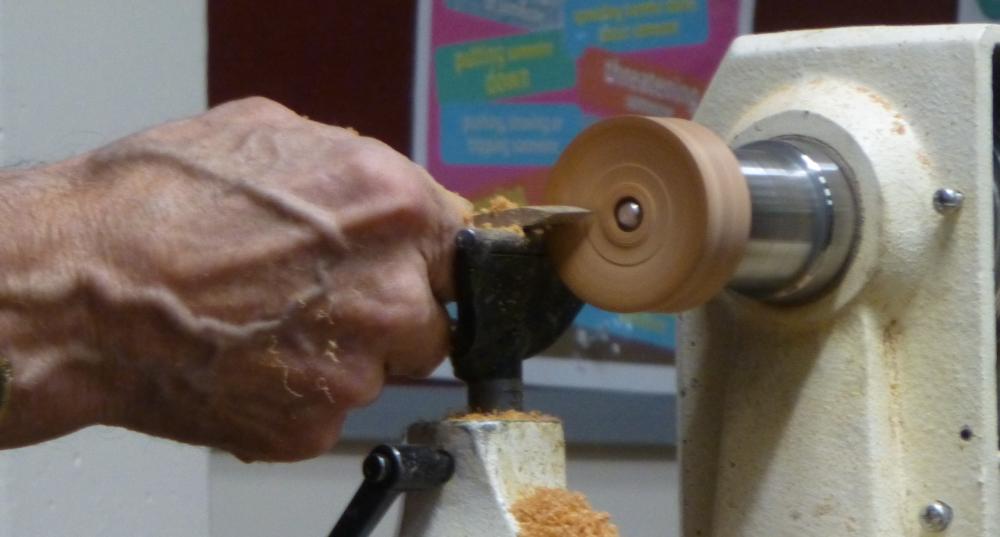
A quick sanding and polish, and the base was reversed onto the chuck where the circumference and top were also sanded and polished. Henry pointed out that you know when the polish is dry when there’s no longer a shadow on the workpiece.
Eyeball
Taking a small round bar of ivory alternative, Henry mounted it in the chuck and used a parting tool to delineate the size of the sphere then drilled a hole in the end – this will be for the pupil and iris of the eye.
Using a simple home-made jig, he drilled a 7mm hole in the side of the blank to suit the tenon on top of the stem.
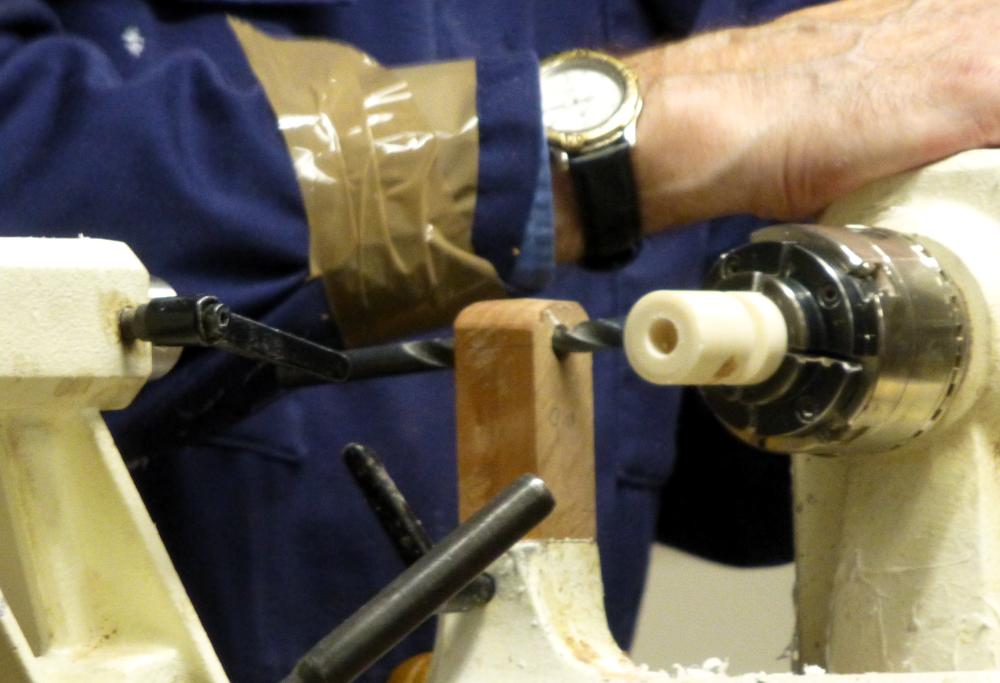
For this latter drilling operation he locked the spindle to ensure a good clean hole.
Mounting a piece of wood in a chuck, he turned it down to diameter to form the iris and glued it into the eyeball (still a cylinder at this point), using the tailstock to press it into position.
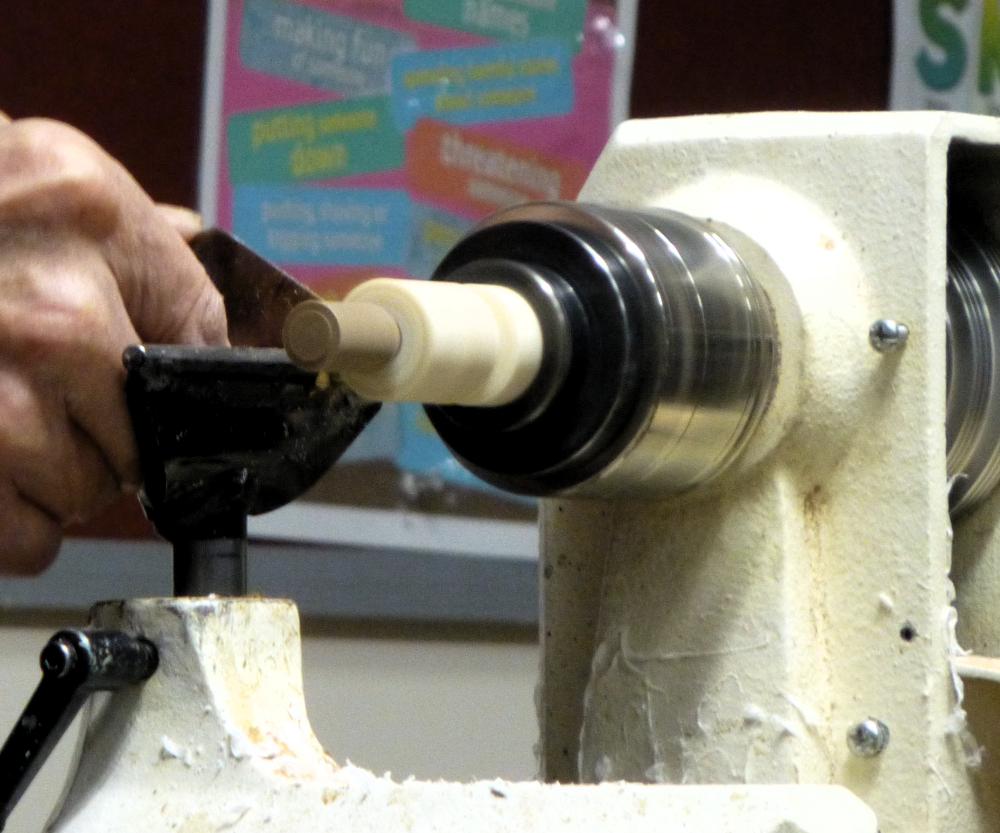
Once this was done, Henry cut off the surplus iris wood and drilled a smaller hole into it. Next, he turned a piece of black wood and glued it into the hole to form the pupil before cutting off the surplus.
With all parts now in place, he rounded over the front of the eyeball and then repeated the operation for the back of the eyeball, using a skew chisel. Happy with the shape, he sanded the eyeball (to 4000 grit!), applied some friction polish and parted it off.
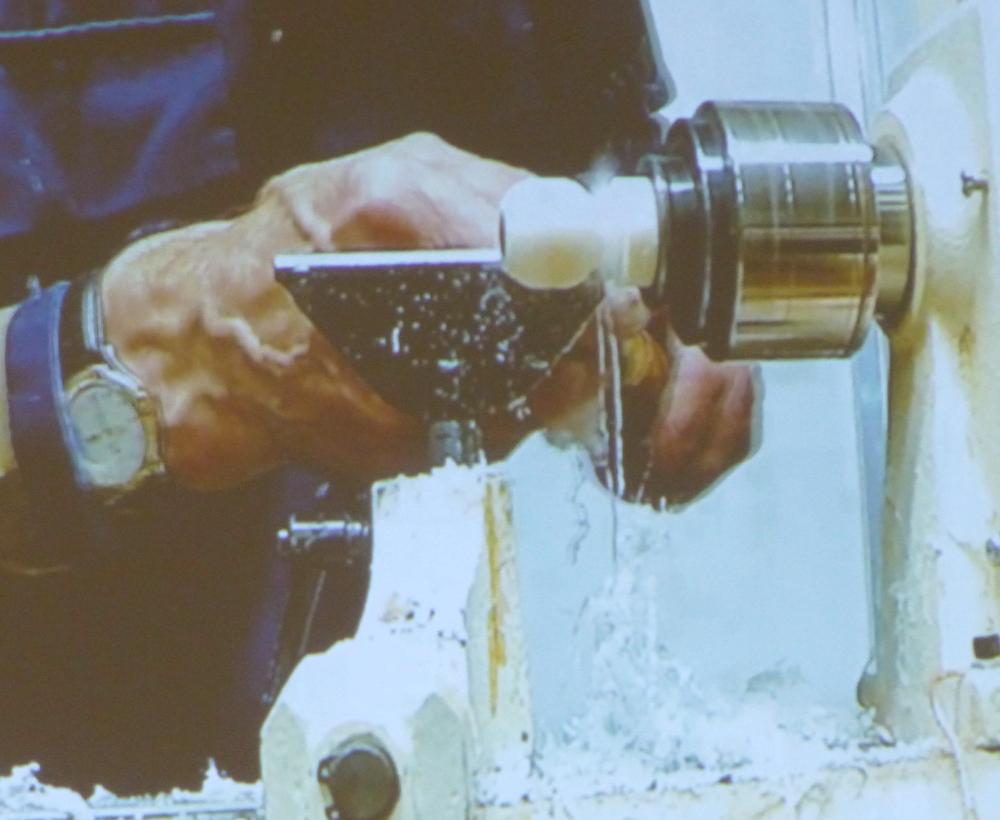
Finally, the stub was removed and rubbed down before assembling the three parts to complete a rather unusual desk ornament!
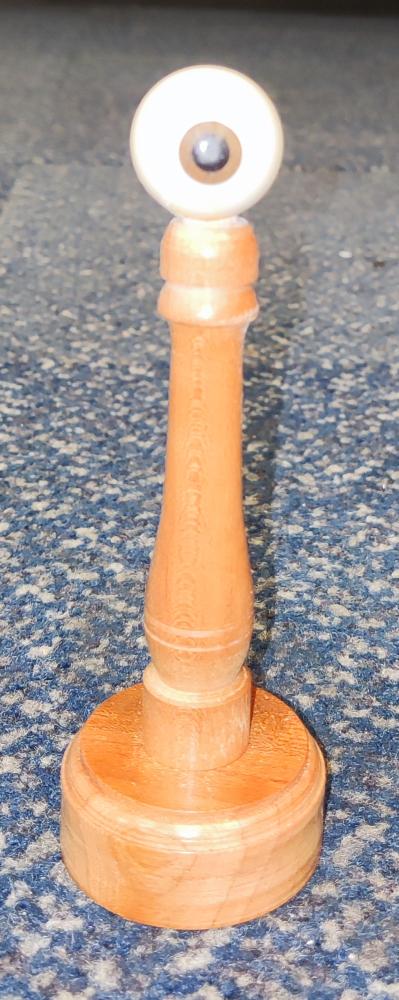