The meeting opened with a welcome from Roger Gilbert, the Chairman, and a few words to let everyone know that MariVe would be co-ordinating the group effort to make a carousel for the 2024 Daventry Woodworks competition. There’s plenty of time yet but we all know how time flies!
There was also a reminder that membership annual subscriptions would be due from next meeting, 6th September.
This evening, Bryan Brumfield demonstrated making a decorative lamp using a DIY Bauble Kit from Emma Cook, the Tiny Turner. These kits are sold by Emma in a number of configurations and may be used to make e.g. Christmas snowmen or simply an attractive light, as in this demo. The kit used here was similar to this one:
To start, a dry old oak blank about 120mm dia x 65mm long for making the stand was mounted in the chuck and a base recess hollowed out. The blank was then drilled for the LED cable – or at least as far as the drill would reach. A through hole is needed so it will be completed from the other end.
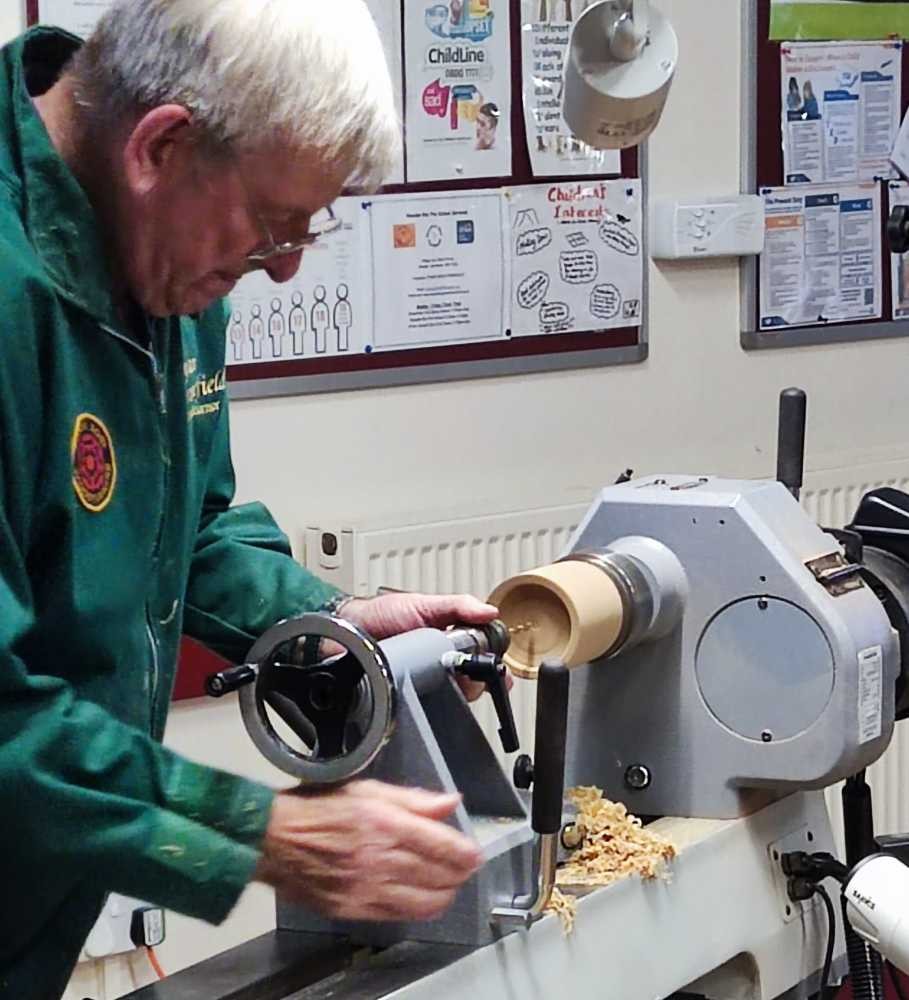
The blank was then reversed onto the expanding chuck jaws, before Bryan removed the tenon and shaped it with gouges.
He then drilled through to meet the hole drilled earlier and thus complete the hole through which the LED cable will pass. Next, he created a recess in the top of the stand in which to sit the bauble.
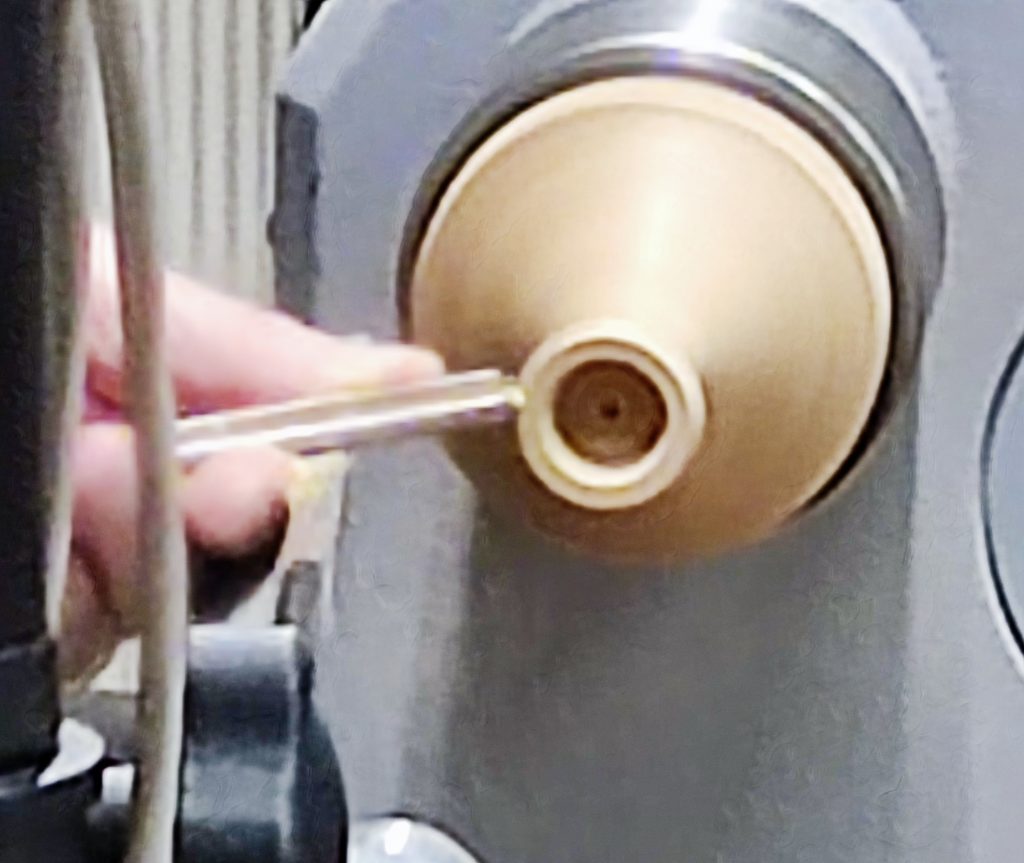
A refining of the shape was followed by sanding and finishing with acrylic sanding sealer and acrylic lacquer before a final polish with a cloth and stick wax.
The stand was now complete so Bryan removed it from the lathe and set about assembling the bauble kit onto the stand.
He fed the LED cable through the centre of the stand and taped the switch/battery assembly into position in the base recess.
Soudal Fix ALL Crystal Clear adhesivewas applied to the recess in the top and he started lowering the bauble towards the recess, all the while feeding the LED lighting cable into the bauble.
This particular type of adhesive is recommended by Emma Cook due to its decent open time and good grab to all types of surface. It can be purchased from Emma’s online shop: https://www.thetinyturner.co.uk/product-page/soudal-fix-all-crystal-adhesive-125ml.
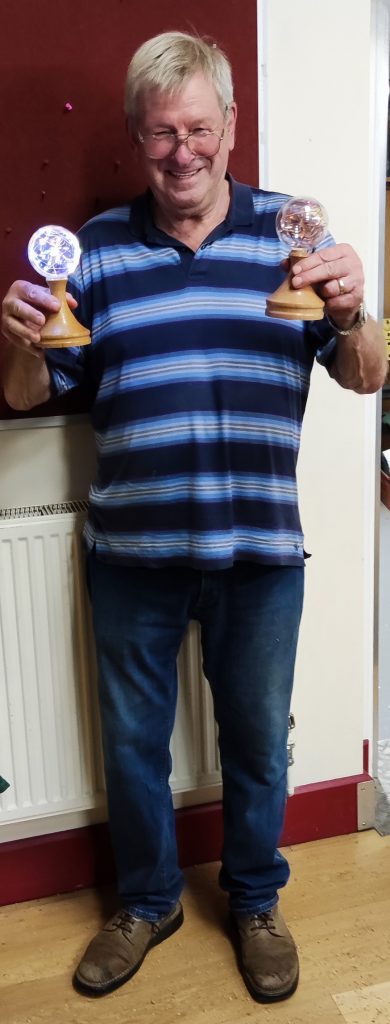
Once the cable was all in place, the bauble was pressed down firmly onto the adhesive. Finally, he turned it on!
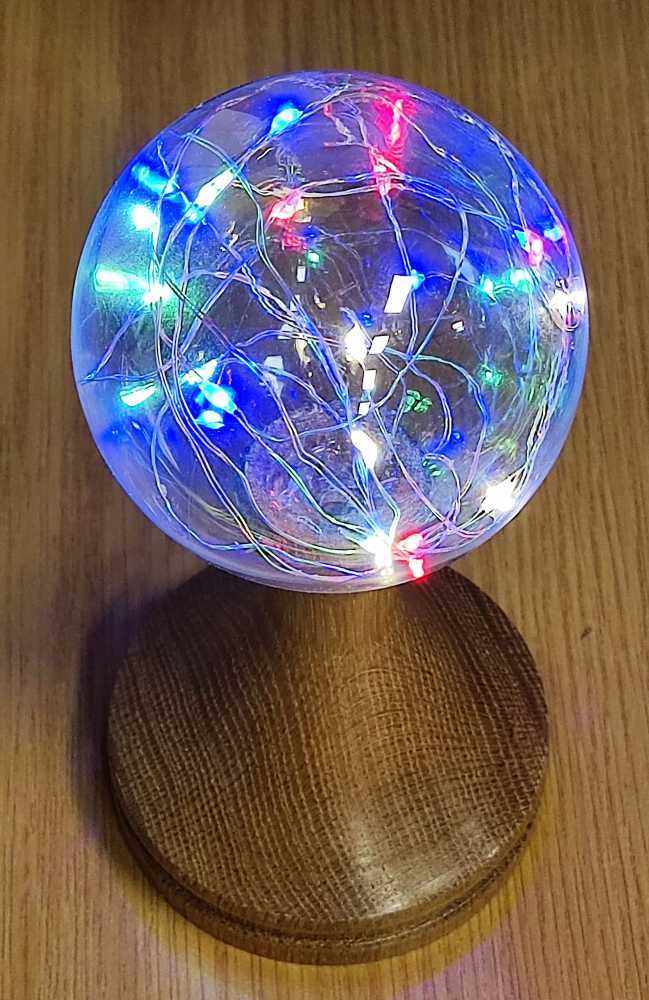